"Auf die Plätze!" Es ist erstaunlich, wie still eine Menge von 80.000 Menschen innerhalb von Sekunden werden kann. Man könnte eine Stecknadel fallen hören, wären da nicht die gedämpften Stimmen der Fernseh- und Radioreporter auf der Pressetribüne und die neun muskulösen Körper, die langsam ihre Startblöcke einnehmen. In den nächsten zehn Sekunden wird sich entscheiden, ob sich die jahrelangen Anstrengungen auszahlen, ob sie diese vielleicht einmalige Chance auf olympischen Ruhm ergreifen werden. "Fertig!"
Um dieses Ziel zu erreichen, mussten die Sportler auf jedes Detail achten und durften sich kaum Fehler erlauben. Tausende von Stunden auf der Bahn. Millionen von Kilos im Fitnessstudio gehoben. Hunderte von schmerzhaften Sitzungen beim Physiotherapeuten. Strenge und minutiöse Zeitpläne für jeden Aspekt des Lebens, vom Schlafverhalten bis zur Ernährung. Ganz zu schweigen von der Ausrüstung: Neben perfekt sitzenden Lauftrikots mussten Dutzende Sprintspike-Paare getestet werden – so leicht, dass sie kaum spürbar sind, aber dennoch eine maximale Kraftübertragung ermöglichen, wenn das Rennen beginnt. Alles in der Hoffnung, dass sich der Aufwand lohnt, dass die menschliche Maschine nicht beschwert wird und zu Höchstleistungen aufläuft, wenn es wirklich darauf ankommt.
Es gibt einen weiteren Bereich, in dem Gewicht und die Liebe zum Detail eine ähnlich große Rolle spielen: Autos. Im Laufe der Jahre haben sie sich zu Spitzensportlern entwickelt, indem sie "Muskeln" aufgebaut haben – allerdings auf Kosten von mehr Masse. Und da Regulierungsbehörden wie die Europäische Union die Hersteller zwingen, den CO2-Fußabdruck ihrer gesamten Flotten zu reduzieren, suchen sie ihrerseits nach Möglichkeiten, die Ausstattung ihrer Spitzensportler zu optimieren – ein Leichtbauteil nach dem anderen. Das Stichwort für die Continental-Trainer.
Partnerschaft mit Leichtbauexperten
Unsere Experten für Gewichtsreduzierung in der Automobilindustrie sitzen im französischen Rennes. Schon vor zehn Jahren suchten sie nach Möglichkeiten, leichte Teile zu entwickeln, die genauso gut funktionieren wie die herkömmlichen Lösungen – und fanden einen möglichen Ansatz in der Luftfahrtindustrie. Dort verwenden Ingenieure schon seit langem Verbundwerkstoffe für große Bauteile. Warum sollte das nicht auch eine Lösung für Automobilanwendungen sein?
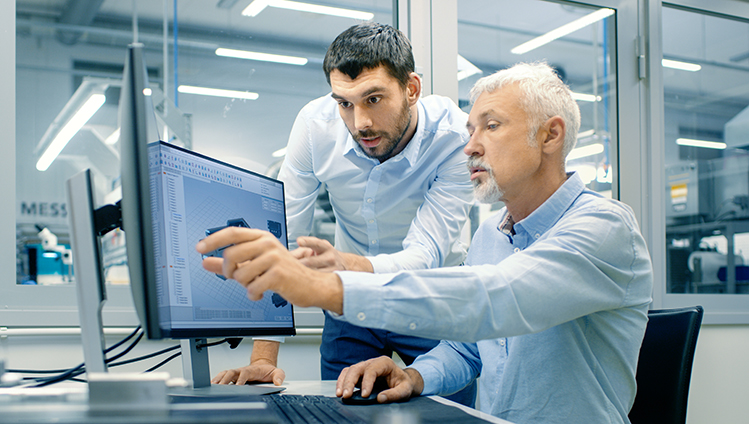
Also taten sie sich mit anderen Pionieren auf dem Gebiet der Leichtbauwerkstoffe zusammen, um ihr Fachwissen über Antivibrationssysteme, Gummi und Thermoplaste mit dem Know-how der Luftfahrtindustrie über thermoplastische Verbundwerkstoffe und automatisierte Faserplatzierungsverfahren zu kombinieren. Dazu kommen die neuesten Forschungserkenntnisse von zwei Universitäten und – voilà – heraus kommt Dynafib, eine neue Materiallösung für Automobilteile.
Starke Teile mit weniger Masse – Dynafib ermöglicht Gewichtsreduzierung im Automobil
Dynafib ist eine Leichtbautechnologie und besteht aus mehreren Lagen von Streifen in einem geschlossenen Ring. Die Streifen bestehen aus Hunderten von sehr langen Glasfasern, die alle in die gleiche Richtung ausgerichtet sind. Sie werden in eine thermoplastische Matrix getränkt und dann mithilfe eines Laserstrahls verschmolzen. Je stärker und stabiler ein Teil sein soll, desto mehr Schichten können verwendet werden. Deshalb eignet sich Dynafib besonders für Teile, die von innen nach außen gerichteten Belastungen standhalten müssen, wie etwa Drehmomentstangen.
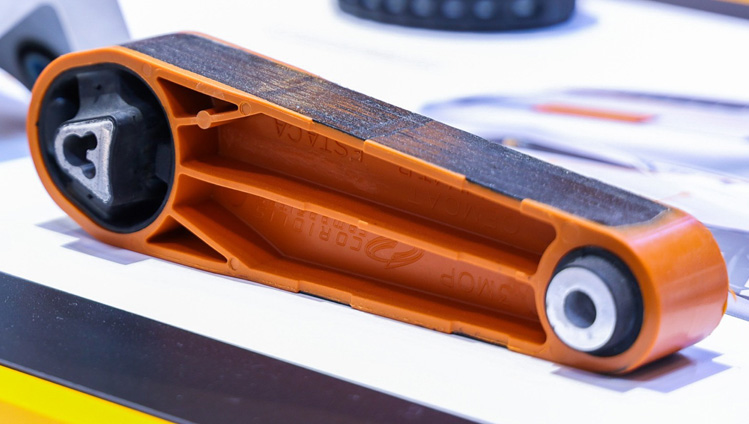
Sie sind ein perfektes Beispiel, um das Potenzial von Dynafib zur Gewichtseinsparung bei gleichbleibender Leistung näher zu beleuchten. Drehmomentstangen bestehen in der Regel aus Stahl oder Aluminium und dämpfen die Auswirkungen des Drehmoments in einem Fahrzeug, indem sie die Übertragung von Vibrationen und Geräuschen verhindern und das Rollen des Motors einschränken. Um alle Teile des Bauteils sicher miteinander zu verbinden, wird die Dynafib-verstärkte Stange mit den beiden Lagerbuchsen kombiniert und dann mit PA umspritzt, was die strukturelle Funktionalität des Teils erhöht. Da die Dynafib-Verstärkung speziell für diese Anwendung entwickelt wurde, verhindert sie das Reißen der Drehmomentstange und verbessert ihre Festigkeit bei deutlich geringerem Gewicht.
Aber wie viel weniger? Nehmen wir eine Drehmomentstange aus Aluminium als Maßstab für unseren Vergleich. Eine Stahlstange mit der gleichen Festigkeit wäre etwa 20 Prozent schwerer. Eine thermoplastische Drehmomentstange, die nicht verstärkt wurde, liegt bei ungefähr 75 Prozent des Gewichts einer Aluminiumstange, hat aber auch nur 50 Prozent ihrer Festigkeit. Nur die leichte Dynafib-Lösung erreicht die gleichen Festigkeitswerte wie die metallischen Varianten und spart dabei rund 50 Prozent des Gewichts im Vergleich zu Aluminium.
Herausforderungen bei der Entwicklung neuer Leichtbautechnologien
Obwohl es sich bei Dynafib um eine hochinnovative Technologie handelt, ist sie leider nicht für jede Anwendung oder jedes Automobilteil geeignet. Im Allgemeinen kommen nur Teile in Frage, die mit einem einzigen geraden Band verstärkt werden können, da sich das Dynafib-Band nicht verdrehen lässt. Außerdem musste der Produktionsprozess durchdacht werden, da wir sicherstellen mussten, dass alle Komponenten durch eine optimale Kunststoffeinspritzung richtig zusammengefügt werden.
Auch die Größe des Bauteils stellt eine Herausforderung dar. In der Luftfahrtindustrie werden schon seit vielen Jahren große Flächen mit weichen Rundungen mit mehreren Lagen multidirektionalem Band hergestellt. Die tatsächliche Herstellung eines so großen, leichten Bauteils erfordert jedoch viel Zeit. Und Zeit ist entscheidend, da sie neben den Kosten eine der Hauptanforderungen der Automobilindustrie bei der Entwicklung von neuen Komponenten ist. Daher ist die Anzahl der Teile, die zu geringen Kosten hergestellt werden müssen, viel höher als die Produktionszahlen für ein Flugzeugcockpit. Damit sich das lohnt, müssen die Dynafib-Drehmomentstangen mit einer hohen Taktzahl von 20 bis 30 Sekunden pro Stück produziert werden.

Es gibt also eine Menge zu bedenken, wenn man ein standardisiertes Metallteil auf neue Leichtbautechnologien umstellen will. Doch während die Dynafib-Drehmomentstange von Continental noch in diesem Frühjahr in die Serienproduktion geht, arbeiten unsere Werkstoff- und Produktexperten in Rennes bereits an der Verschlankung anderer Automobilkomponenten wie Lenkerarme und Luftfedern, bei denen wir hoffen, durch den Einsatz von Dynafib etwa ein Drittel ihres ursprünglichen Gewichts einzusparen.
Und während sich die Dynafib-Trainer bisher auf Personenkraftwagen konzentrierten, wagen sie sich bereits in die Welt hinaus in der Überzeugung, dass es auch andere Fahrzeuge gibt, die von einer Gewichtsreduzierung profitieren würden: Lastkraftwagen, landwirtschaftliche Fahrzeuge, Baumaschinen, Straßenbahnen und Züge, Fahrräder und andere Fortbewegunbsmittell. Ganz zu schweigen von anderen industriellen Anwendungen außerhalb der Mobilität – die Bandbreite der Möglichkeiten für Leichtbaulösungen ist fast so groß wie die Zahl der Disziplinen im magischen Sommer 2024 in der französischen Hauptstadt.
Die Zukunft: nachhaltige Leichtbaulösungen
Abnehmen ist natürlich kein Selbstzweck, weder für Leichtathleten noch für Autos. Für die OEMs hat die Übung einen Zweck: Nachhaltigkeit. Ein geringeres Fahrzeuggewicht führt zu weniger Kraftstoffverbrauch und damit zu weniger CO2-Emissionen. Aber wir bei Continental schauen nicht nur auf die nachgelagerte Wertschöpfungskette, sondern auch auf unsere eigenen Materialien, Lösungen und Prozesse. Das Tolle an Dynafib ist nämlich, dass der Produktionsprozess selbst nicht viel Energie verbraucht. Dennoch ist die gesamte CO2-Bilanz noch nicht so, wie wir sie gerne hätten, vor allem wegen der verwendeten Materialien: Glasfasern und neue Thermoplaste.
Auch daran arbeiten unsere Dynafib-Experten in Rennes bereits. Sie hoffen, dass sie bereits im nächsten Jahr eine neue Leichtbaulösung auf der Grundlage der Dynafib-Technologie mit biobasierten Materialien und recycelten Polymeren einführen können, die den gesamten Kohlenstoff-Fußabdruck auf einen Bruchteil des heutigen Wertes reduzieren würde. Ein echtes Leichtgewicht mit voller Power. Und auf dem Weg dorthin werden vielleicht einige von ihnen unter den 80.000 Fans sein, die in Jubel ausbrechen, wenn der Startschuss in Paris fällt. "Los!"