La Norvège est un pays de superlatifs. Avec près de 240 000 îles1, 1 000 fjords2, 2 000 chutes d’eau3 et 200 000 élans4, on y trouve également de nombreuses voitures électriques. Ce n’est pas un miracle, mais une stratégie : depuis 30 ans, le pays encourage la mobilité électrique car l’électricité verte est souvent moins chère que l’essence ou le diesel en Scandinavie. Les héritiers des Vikings ont également les plus grandes ambitions pour l’avenir : d’ici 2025 au plus tard, plus aucune voiture neuve ou véhicule utilitaire léger à moteur à combustion ne doit être vendu. Les conditions sont donc parfaites pour une transformation vers une mobilité durable et à faibles émissions.
Vraiment ? Car en réalité, les conditions météorologiques ne sont pas du tout optimales pour la technologie de la mobilité électrique, dans un pays où il peut y avoir jusqu’à onze mètres de neige en hiver, et où les températures peuvent descendre jusqu’à moins 40°C . Pour que la batterie, qui est ultrasensible puisse malgré tout conserver toute sa puissance à des températures extrêmes, nos ingénieurs doivent repenser entièrement la gestion de la température dans le véhicule.
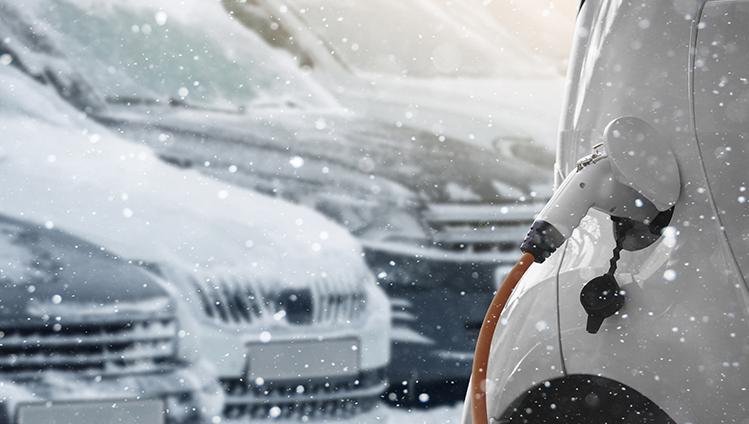
Avoir froid dans une voiture électrique ? Non, merci !
Ceux qui ont déjà fait du ski le savent : les batteries sont fragiles. Cela vaut aussi bien pour les batteries des smartphones que pour celles des vélos électriques ou des véhicules électriques. Elles supportent difficilement la chaleur de l’été, le froid de l’hiver, les conditions extrêmes. En effet, le froid en particulier ralentit les processus électrochimiques, diminue la tension de la batterie et une décharge profonde, dommageable pour la batterie, risque de se produire. Le problème est que l’énergie électrique perdue à cause d’une mauvaise température ne peut être récupérée. C’est pourquoi les performances d’une batterie d’un véhicule électrique sont maximales dans une plage de température comprise entre 15°C et 40°C . Et c’est précisément pour cette raison que nos systèmes de conduite ont une influence directe sur l’autonomie des voitures électriques.
Une longue conduite de refroidissement
En principe, la construction des véhicules électriques est nettement moins complexe que celle des véhicules à moteur à combustion : une voiture à essence avec boîte de vitesses manuelle, par exemple, compte environ 1 400 pièces, alors qu’une voiture électrique n’en compte que 200. Exception : les conduites de refroidissement et de chaleur. En effet, alors que dans le véhicule à combustion, seul le moteur lui-même doit être refroidi et que la chaleur produite peut être utilisée pour le chauffage de la cabine, le réseau de conduites dans le véhicule électrique est nettement plus compliqué. Ici, la température doit être gérée pour plusieurs circuits, pour le groupe motopropulseur, la climatisation et enfin la batterie.
Selon la température extérieure, la batterie a donc besoin soit de refroidissement, soit de chaleur. En règle générale, on utilise aujourd’hui des systèmes séparés, reliés par un échangeur de chaleur. Et c’est ainsi que la longueur totale des conduites double par rapport au véhicule à combustion, pour atteindre près de 30 mètres. Il en va de même pour le nombre de connecteurs, de raccords rapides et d’attaches nécessaires. Dans un gros véhicule utilitaire, cela peut représenter près de 100 tubes et tuyaux individuels, plus autant d’éléments de transition.
L’essentiel est d’être étanche
La caractéristique la plus importante pour les câbles dans les véhicules à propulsion électrique : une étanchéité absolue. En effet, un mélange d’eau et de liquide de refroidissement, comme le glycol, circule dans les tuyaux et les tubes. C’est pourquoi les matériaux utilisés doivent également présenter la résistance chimique correspondante. Par le passé, on utilisait des matériaux EPDM pour les tuyaux flexibles, et de l’aluminium ou de l’acier pour les tuyaux plus solides. Aujourd’hui, les mélanges de caoutchouc réticulés par peroxyde sont de plus en plus remplacés par des élastomères thermoplastiques, l’aluminium et l’acier sont remplacés par des matières plastiques PA, PP ou PPS. Selon les exigences des équipementiers, ces matériaux peuvent également être combinés entre eux pour une solution optimale et reliés par des connecteurs appropriés.

D’ailleurs, la collaboration avec les fabricants requiert des expertises tout à fait différentes. Les OEM établis ont souvent déjà une idée très détaillée et concrète de la conception, de sorte que le temps est plutôt investi dans le développement et les validations de différentes options de matériaux. Nos clients start-up dans le domaine de l’eMobilité laissent volontiers plus de liberté de conception à nos ingénieurs et s’en remettent à notre savoir-faire de longue date pour le choix des matériaux pour les tuyaux, tubes et autres.
Durabilité + électromobilité = avenir
Comme toujours dans l’électromobilité, le thème de la durabilité joue également un rôle particulier en ce qui concerne les matériaux. Et pas seulement parce que les consommateurs finaux accordent de plus en plus d’importance à la préservation des ressources et à la durabilité des produits. Heureusement, les conduites d’un véhicule sont généralement conçues de manière à ne pas devoir être remplacées. Cela suffit à réduire la consommation de ressources. De plus, nos développeurs font particulièrement attention au poids des composants. En effet, en raison du poids élevé de la batterie, chaque gramme possible doit être économisé ailleurs. Grâce à de nouveaux matériaux qui, malgré une épaisseur de paroi plus faible, sont aussi solides et étanches que leurs prédécesseurs, nous avons déjà pu économiser plus de 50 % de poids en comparaison.
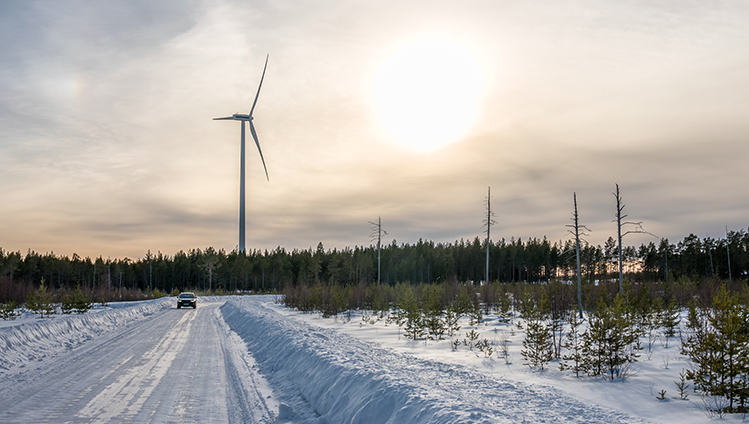
La durabilité est également un atout dans la production propre à Continental. Nous voulons neutraliser notre empreinte en CO2 dans le monde entier par des émissions négatives – y compris la production, la chaîne d’approvisionnement et la fin de la phase d’utilisation. Nous nous concentrons sur les véhicules qui n’émettent pas de gaz d’échappement. Et ce n’est pas une mince affaire. En effet, la plupart des conduites et des tuyaux, qu’il s’agisse d’EPDM, de TPE ou d’autres matières plastiques, ne sont pas constitués d’une seule couche et le support de résistance incorporé est difficile à séparer des autres couches. Néanmoins, les monocouches sont tout à fait envisageables. Des granulés recyclés, par exemple à partir de vieilles bouteilles en PET, pourraient également être utilisés. Nos experts en matériaux estiment qu’il existe encore un grand potentiel inexploité dans ce domaine. Et ici la boucle sera bouclée : la Norvège prend également ses obligations de recyclage très au sérieux. La première usine de recyclage de batteries de voitures électriques devrait bientôt entrer en service à Fredrikstad.
1https://www.laenderdaten.info/inseln-nach-land
2https://www.visitnorway.com/things-to-do/nature-attractions/fjords/the-fjords-explained/
3https://www.worldwaterfalldatabase.com/country/Norway/list
4https://www.nordlandblog.de/elche-norwegen-beobachtung-safari/